Laser plastic welding uses precisely focused energy to create particulate-free hermetic seals in wearable medical device packages without damaging sensitive electronics and sensors.
The Use of Thermoplastic Materials in Wearable Medical Devices is Growing . . .
. . . as medical design engineers look for a flexible, high-yield path to increased yields and reliability. New Laser plastic welding is the perfect assembly technique for wearable devices where high yields mean significant margin improvements, weight savings, reduced bill of materials, stronger bonds and reduced assembly times.
Laser plastic welding is used to produce strong, hermetic seals on medical device packages.
Welding of Engineering Polymers
Laser plastic welding can weld any thermoplastic polymer, including up to 30% glass filled nylons; PA-6, PA-66, PBT, PET, PC, PBT/ABS alloys, and many others.
Major Benefits of Laser Plastic Welding to Assembly Plastic Wearable Medical Devices
Laser plastic welding offers a high degree of flexibility to rapidly and inexpensively change over to new designs and adapt to new product form factors by simply changing the tooling and uploading the latest CAD designs into the machine.
Laser plastic welding machines are available in the right size to fit your needs with machines to accommodate part sizes from 100 mm x 100 mm to 1,000 mm x 750 mm.
Key Advantages for Laser Welding of Plastic Fluid Components
Particle Free
Laser plastic welding is a particle-free joining process compared to ultrasonic or vibration welding so your assembly process will not contribute to particulate contamination from the manufacturing process.
Protect Sensitive Electronics and Sensors
Exceedingly Strong
The dynamic process of quasi-simultaneous welding supplies additional material to the joint, much like a welding rod in metal welding, to create joints that exceed the strength of the molded parts themselves.Significant Savings on BOM and Labor
The laser plastic welding assembly method allows designs without the need for screws that reduces the bill of materials (BOM) and therefore costs compared to components that are secured with screws. Laser plastic welding is a faster assembly method compared to UV cured adhesives and eliminates the costly maintenance and mess of glue dispensing and curing.
Fast Cycle Times
Depending on the part size, laser plastic welding machines from LPKF has cycle time from a few seconds on small parts (100 mm x 100 mm) to under a minute for large parts (500 x 350 mm).
Laser Welding Machine Configurations
Off the Shelf Solutions
LPKF has a wide range of highly flexible, standardized machines with custom tooling to rapidly change from one part to another with a simple CAD import and quick-change tooling. Laser welding machines come in four different standard sizes to match your part size and budget. LPKF has a complete line of standalone and integrated laser plastic welding solutions to fit your R&D, development and low to high volume manufacturing requirements.
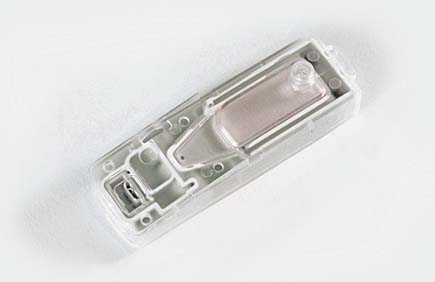
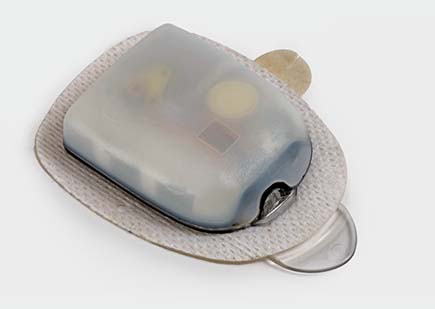
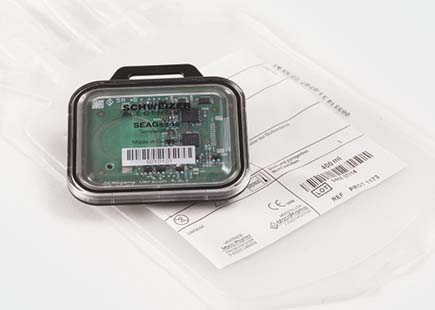
Custom Solutions
LPKF also offers custom engineered solutions with multiple lasers, mirrored tooling, clamping systems, and conveyor systems to that are turnkey, drop-in solutions.
Manage Risks
LPKF systems are backed by process development, prototyping and validated production recipes so that you don’t have to worry about the details of laser welding. Let LPKF worry about the welding, so you don’t have to. LPKF has years of experience designing and building laser plastic welding systems for the assembly of wearable medical devices. LPKF machines are used to make hundreds of millions of wearable devices annually. LPKF’s Getting Started program provides you with rapid materials and design evaluation and guidance to manage risk right from the start. For one low price, you can have a customized development package that includes material tests, design evaluations and guidance, prototype tooling and services to deliver proof of concept parts and prototypes in three to four weeks.
Want to Know More about Laser Plastic Welded Wearable Medical Devices?
Please complete the form below and our experts will contact you to discuss your specific application.